Transform Your Injection Molding Design Process with Simulation
Thank you for attending | 25th Oct.
Webinar recording will be available soon.
Learn how to reduce lengthy mold trials, resolve manufacturing defects and reduce costs.
Designing cost effective injection molded parts can be a challenging process where unexpected warping, sink marks and other manufacturing issues are discovered late. Part and mold designers are forced to make design changes, leading to product delays and increased material scrappage. Plastic injection molding companies are turning to manufacturing simulation technologies to address this challenge; identifying and eliminating potential manufacturing defects before any physical molds or parts are produced.
This free to attend webinar demonstrated how plastic injection molding companies are utilising Altair® Inspire™ Mold to improve their mold and part creation. During the one hour session, we demonstrated how placing easy to use yet powerful simulation solutions in the hands of designers and product engineers early in the development cycle can enable rapid exploration of options to improve product performance while reducing scrap and tooling rework costs.
Attendees learnt how to:
- Use Inspire Mold's intuitive interface to determine and optimise part moldability
- Identify and fix common molding defects such as sink marks, warpage, Air traps, Weld Lines etc.
- Use intuitive tools to predict fill time and melt temperature.
What's included in Altair® Inspire™ Mold?
- New workflow supporting quick moldability checks as well as advanced simulations
- Access to a large editable material database
- Filling and fiber orientation, packing cooling and warpage analysis.
Speakers
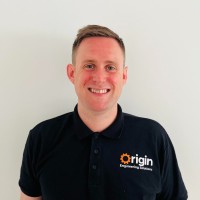
Rob Shropshire
Director
Origin Engineering Solutions
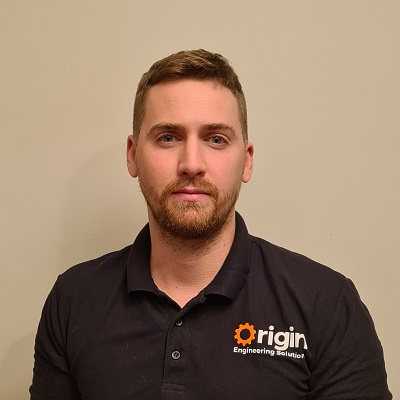
Tim Dukes
Director
Origin Engineering Solutions
*Free trial offer for new clients only. Terms & Conditions apply.